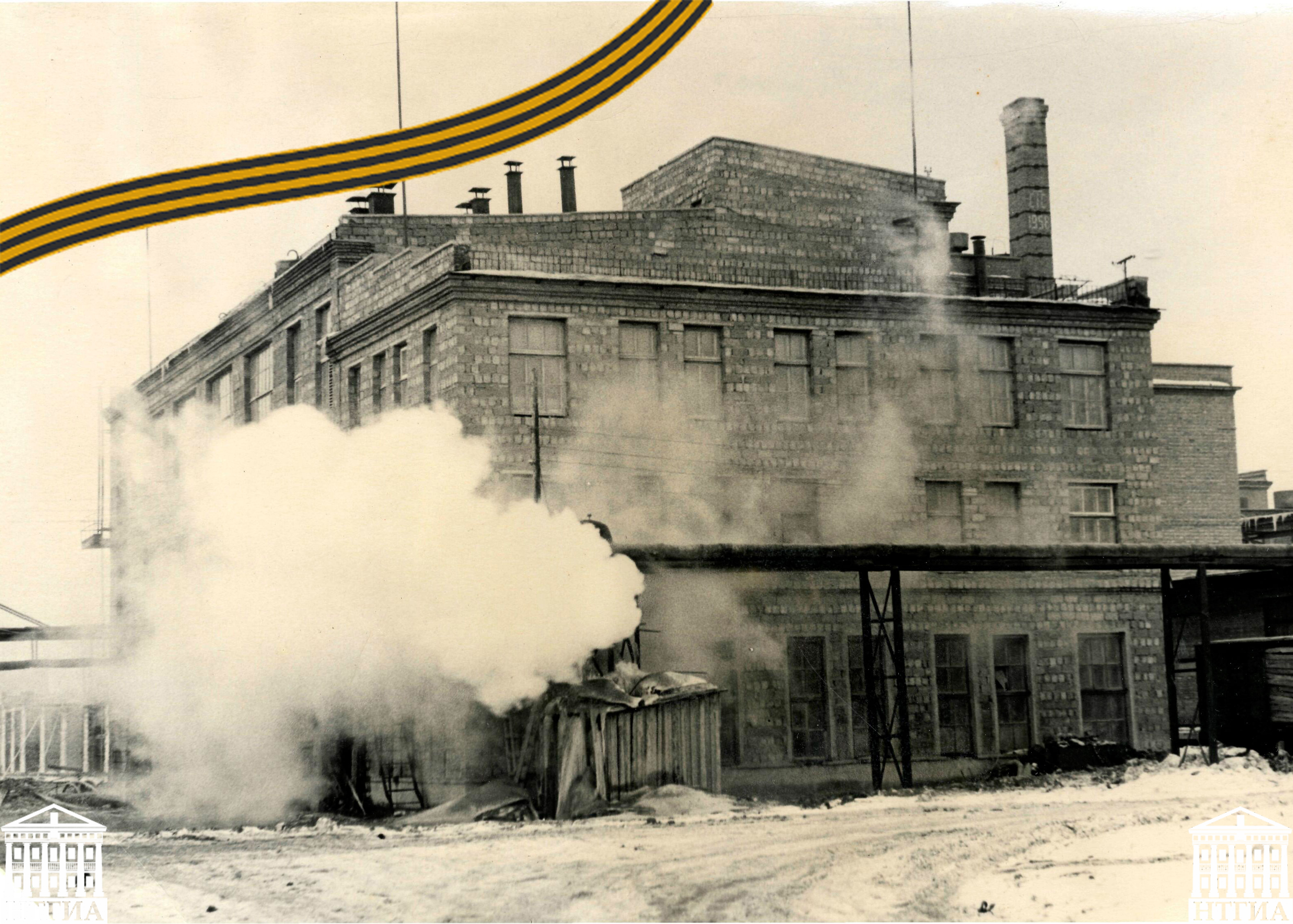
В годы Великой Отечественной войны Уральский регион был не только крупнейшим центром оборонного машиностроения, черной и цветной металлургии, но и важнейшей химической базой военной индустрии.
На площадке торфохимического завода основанного в Нижнем Тагиле в 1938 году, было смонтировано оборудование Ленинградского, Московского экспериментального и Карачаровского заводов пластмасс. В IV квартале 1941 года были введены в эксплуатацию фенольный цех и цеха по прессованию и обработке пластмассовых изделий.
На основании приказа Наркомата химической промышленности СССР от 06.01.1942 года № 1 торфохимический завод стал именоваться Нижнетагильским заводом пластмасс № 767. Основной продукцией предприятия стали детали для танков, самолетов, боеприпасов, пробки для авиабомб, изделия для полевых телефонов и другое. Но все же приоритетным направлением было производство деталей минных взрывателей.
В производстве деталей минных взрывателей СБ-1 и МП-8 пластические массы являлись полноценным заменителем металлов. Поэтому значение производства пластмассовых деталей было чрезвычайно велико для фронта и всего народного хозяйства. В то время в Свердловской области это был единственный завод, который выпускал изделия для минного взрывателя и обеспечивал ими другие оборонные предприятия.
Детали минного взрывателя изготавливали из тонкого и прочного пластмасса, а именно оболочку взрывателя, предназначенного для приведения в действие боеприпаса.
В документах архивного фонда Акционерного общества открытого типа «Уралхимпласт» имеются материалы совещания представителей заводов Главхимпласт по производству пластмассовых деталей минного взрывателя СБ-1 и МП-8. Развитие производства этих деталей за первые два года войны характеризовались следующими цифрами: если принять выпуск 1941 года за 100%, то в 1942 году промышленность пластических масс выпустила этих деталей – 400%.
Но, несмотря на высокие показатели выпуска продукции, Нижнетагильский завод пластмасс сталкивался с некоторыми трудностями. Так, в годовых отчетах завода в первые годы войны прослеживается следующее: инструментальный цех завода совершенно не использовался, обработка деталей производилась на ручных станках, система технического контроля была не налажена, а транспортировка изделий осуществлялась в случайной таре. Все это определяло и большой процент брака продукции, и, соответственно, невыполнение плановых показателей. Основным фактором являлось использование 9-местных прессформ, установленных на 200-тонных прессах, оказывающих большое давление на гнезда прессформ, образуя тем самым завышение высоты изделия и неровные края на резьбе.
Тем не менее, устраняя недостатки в работе, совершенствуя технологический процесс, применяя рекомендуемые 19-местные прессформы, завод сумел наладить производство и наряду с другими предприятиями химической промышленности обеспечить фронт качественной продукцией.
Продолжение следует
При любом воспроизведении информации ссылка на сайт обязательна